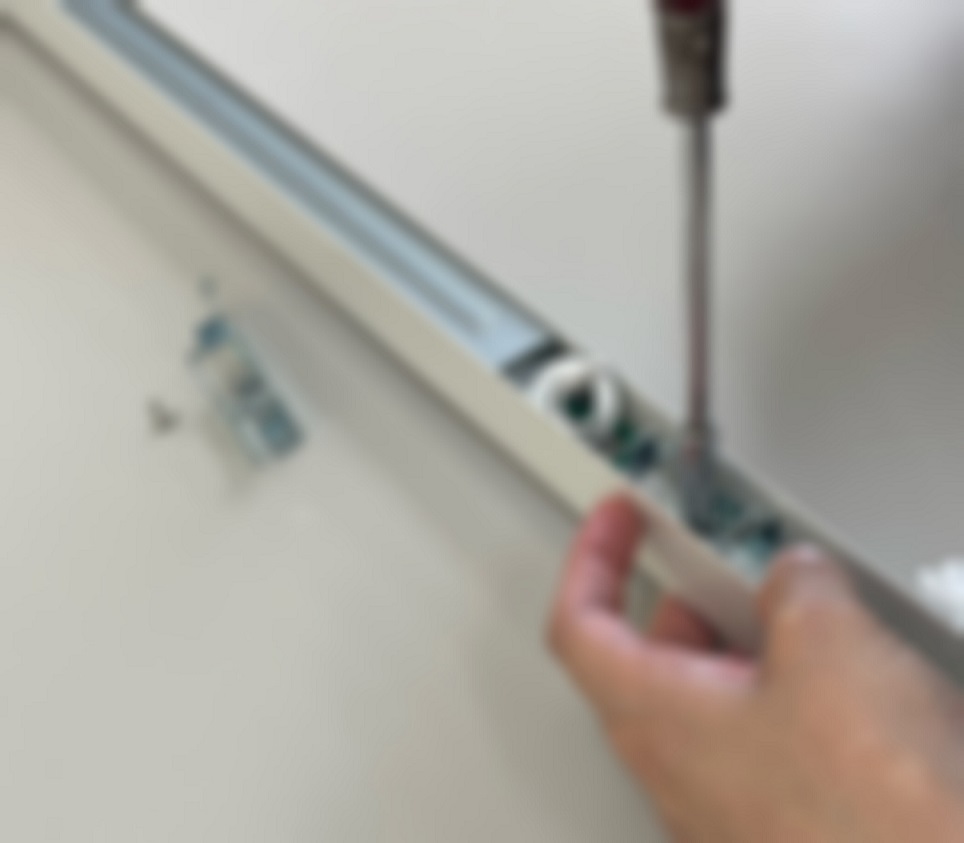
会社説明会や動画だけではなかなか知ることができない、エンジニアの業務。
製品開発に携わる新入社員の瑠璃川が、1人前のエンジニアとして自身が手掛けた製品が世に出るまでを記す。
ゆえにこの連載は来月で終わるかもしれないし、10年かかるかもしれない。
Work at ADN -THE REAL-を通してADN発、新入社員成長ドキュメンタリーを紹介します。
2024年10月 配属15ヶ月目
瑠璃川はこれまで、急遽変更になった製品仕様に合わせて設計案の見直しや試作の準備を進めてきた。
試作では製造現場で実際に組立を行いながら、製造現場での組立易さや工数をはじめとした生産性、想定している組立方法で品質面に問題がないかなどの確認を行う。
彼女と教育係が立ち会いの元で行われた試作だったが、組立を進めていく中で思わぬ問題が発生した。
今回の特注案件は既存製品と比較すると2cm程高さがある設計であったため、製造現場で使用しているナットを締める電動ドライバーに取り付けることができる既製品のビットでは長さが足りないことが判明したのである。
反対側から留めようとするとナット部分が外側に飛び出してしまうため、工具を用意するか設計案を見直すしか方法はない。さらにビット部分は特注になるため、製作を急いだとしても期日に間に合う可能性は低かった。
しかし、顧客に良いものを早く、安く提供するためにも、組立性を妥協したくはなかった。
彼女は、ナットや電動ドライバーを使用せずに組立性を維持する方法はないか教育係と共に検証を重ねていった。
彼女が設計を行っている製品は、天井などへの埋め込みが可能な製品であるため、ねじがアルミ部材の高さを僅かに超えただけでも取り付けに支障が出てしまう。
そのため、想定していた案ではアルミ部材の高さを超えないように上面をフラットに加工したオリジナルのねじを使用していた。このねじをナットを使わないもので代用できないかと彼女はトライ&エラーを繰り返していった。
しかし、改良案は中々見つからない。ブラインドリベットは挿入してシャフトを引き抜くだけで部材の締結が行えるため、ねじを使うよりも組立易い設計になるが、頭部がアルミ部材の高さを超えてしまうなどデザイン性への影響が大きかった。
また、Sタイトのタッピンねじは自分でねじ穴を作りながら締結を行うためナットを使わず、部材の反対側から差し込めるため電動ドライバーの使用や工数削減が可能だったが、頭部の部分を特注にする必要があったため使用は難しいと判断された。
どのような状況であっても顧客の元に最高の製品を届けるために、ビットが間に合うかを確認しながら、彼女は教育係と共にあらゆる可能性を検討し、関係部門を巻き込んで試作検証を続けている。
製造現場の電動ドライバーが使用できなかったことで、彼女は顧客に良いものを早く、安く提供するために、あらゆる事態を想定して対策を行う必要性を痛感した。
若手の挑戦を支える当社の教育環境に支えられ、躓きながらも彼女は挑戦を続けている。
次回、彼女が手掛ける案件は無事に量産へ移行することができるのか、目が離せない。
製品開発に携わる新入社員の瑠璃川が、1人前のエンジニアとして自身が手掛けた製品が世に出るまでを記す。
ゆえにこの連載は来月で終わるかもしれないし、10年かかるかもしれない。
Work at ADN -THE REAL-を通してADN発、新入社員成長ドキュメンタリーを紹介します。
2024年10月 配属15ヶ月目
瑠璃川はこれまで、急遽変更になった製品仕様に合わせて設計案の見直しや試作の準備を進めてきた。
試作では製造現場で実際に組立を行いながら、製造現場での組立易さや工数をはじめとした生産性、想定している組立方法で品質面に問題がないかなどの確認を行う。
彼女と教育係が立ち会いの元で行われた試作だったが、組立を進めていく中で思わぬ問題が発生した。
今回の特注案件は既存製品と比較すると2cm程高さがある設計であったため、製造現場で使用しているナットを締める電動ドライバーに取り付けることができる既製品のビットでは長さが足りないことが判明したのである。
反対側から留めようとするとナット部分が外側に飛び出してしまうため、工具を用意するか設計案を見直すしか方法はない。さらにビット部分は特注になるため、製作を急いだとしても期日に間に合う可能性は低かった。
しかし、顧客に良いものを早く、安く提供するためにも、組立性を妥協したくはなかった。
彼女は、ナットや電動ドライバーを使用せずに組立性を維持する方法はないか教育係と共に検証を重ねていった。
彼女が設計を行っている製品は、天井などへの埋め込みが可能な製品であるため、ねじがアルミ部材の高さを僅かに超えただけでも取り付けに支障が出てしまう。
そのため、想定していた案ではアルミ部材の高さを超えないように上面をフラットに加工したオリジナルのねじを使用していた。このねじをナットを使わないもので代用できないかと彼女はトライ&エラーを繰り返していった。
しかし、改良案は中々見つからない。ブラインドリベットは挿入してシャフトを引き抜くだけで部材の締結が行えるため、ねじを使うよりも組立易い設計になるが、頭部がアルミ部材の高さを超えてしまうなどデザイン性への影響が大きかった。
また、Sタイトのタッピンねじは自分でねじ穴を作りながら締結を行うためナットを使わず、部材の反対側から差し込めるため電動ドライバーの使用や工数削減が可能だったが、頭部の部分を特注にする必要があったため使用は難しいと判断された。
どのような状況であっても顧客の元に最高の製品を届けるために、ビットが間に合うかを確認しながら、彼女は教育係と共にあらゆる可能性を検討し、関係部門を巻き込んで試作検証を続けている。
製造現場の電動ドライバーが使用できなかったことで、彼女は顧客に良いものを早く、安く提供するために、あらゆる事態を想定して対策を行う必要性を痛感した。
若手の挑戦を支える当社の教育環境に支えられ、躓きながらも彼女は挑戦を続けている。
次回、彼女が手掛ける案件は無事に量産へ移行することができるのか、目が離せない。