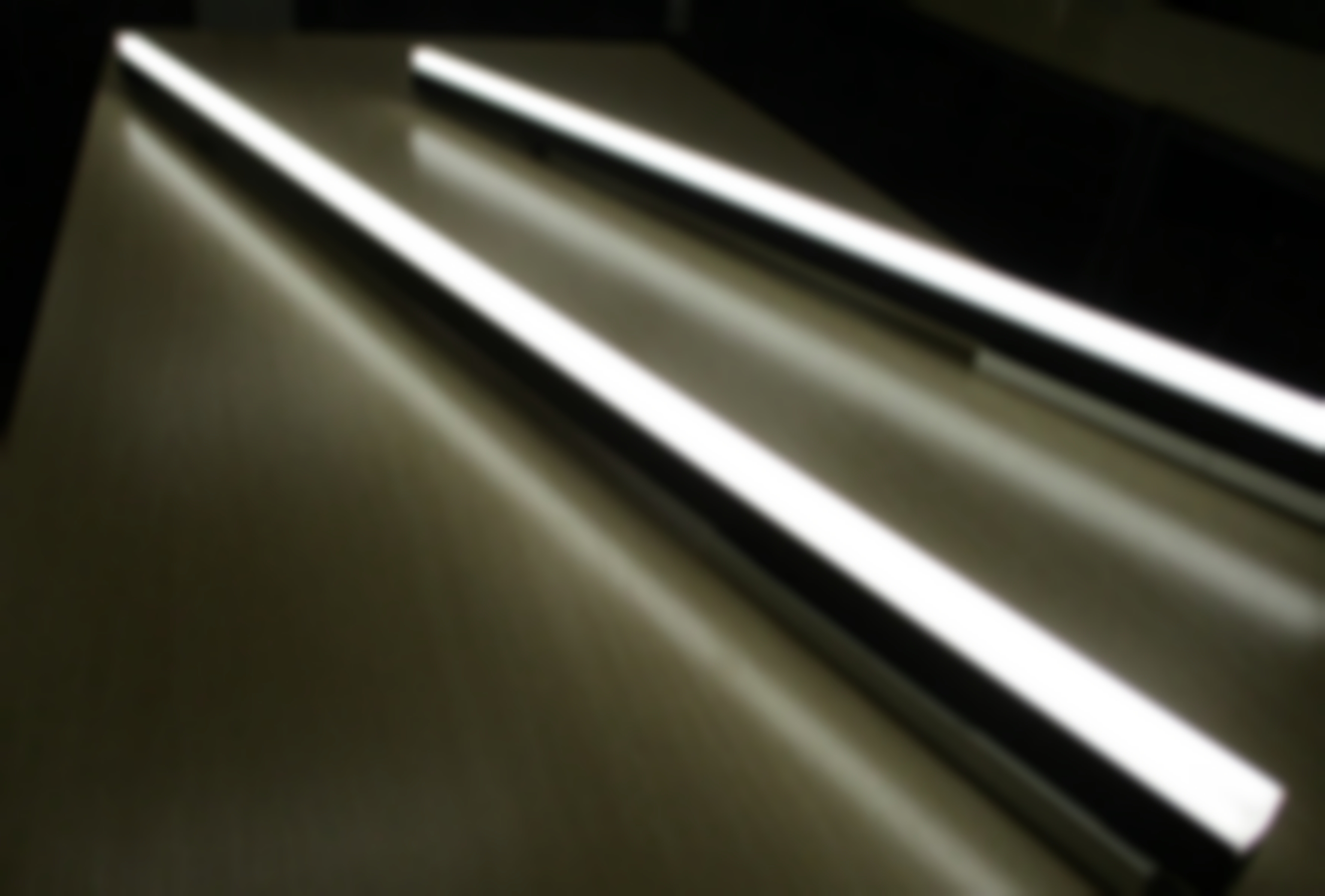
会社説明会や動画だけではなかなか知ることができない、エンジニアの業務。
製品開発に携わる新入社員の瑠璃川が、1人前のエンジニアとして自身が手掛けた製品が世に出るまでを記す。
ゆえにこの連載は来月で終わるかもしれないし、10年かかるかもしれない。
Work at ADN -THE REAL-を通してADN発、新入社員成長ドキュメンタリーを紹介します。
2024年11月 配属16ヶ月目
瑠璃川はこれまで、ナットを締める電動ドライバーに取り付けるビットが間に合うかを確認しながら、組立方法の検証を続けていた。
生産開始予定日が近づく中、彼女の元にビットの外注先から連絡があったが、やはり量産開始の期日までにビットが届かないことが確実になった。
彼女は生産開始までの期日を考慮して、事前検証で検討していた案の1つである「ビットの代わりにボックスドライバーを使用して組立を行う」という方法で生産を進める決断をした。
事前検証で、多少工数が増えるもののデザイン性や品質面の問題がないことを確認していたため、すぐに量産段階に移行できた。
量産開始にあたっては、自身が原設計を手掛けた製品の最終段階を見届けるためにDNライティングの原設計担当者も立ち合いを行っており、案件を進める中で生じたお互いの疑問点や今後の要望など細かい点を意見交換することができた。
今回の特注案件は、既存の調光可能な製品に調色機能を追加するというものだった。
LED照明器具の光は器具内の基盤に取り付けられたLEDチップの色や明るさの違いによって変化する。しかし、LEDチップ自体に色味を変化させる機能はなく、チップは1色にしか光らない。
そのため、調色可能な製品にする場合は基板に色の違う2種類のチップを交互に配列する。
色を切り替えるつまみを回した時に違う色のLEDチップが光る設計にすることで、色の変化を実現するのである。
しかし、LEDチップへの電流の調整や切り替えを行う必要があるため回路設計がより複雑になり、調色機能がない製品と比較して電源装置本体が1.1~1.2㎝ほど大きくなる。
また、電源と基板を繋ぐ電線の数も増えてリードが太くなるため、組み立てる際に本体の中に収めづらくなってしまう。
顧客のニーズを製品に最大限反映するためにも照明器具本体の部材の大きさは変更できないため、リードの長さなどを微調整することで既存製品と同じ組立性を維持しながらデザイン性や品質を維持することができる。
当社に送られてくるデータでは顧客から出された要望をどのように原設計に反映しているか詳細には読み取れないため、今後より一層顧客のニーズに応えた量産設計を行うための勉強になったと彼女は語った。
DNLグループは、マザーファクトリーでもある当社を様々な角度から有効活用して顧客の声をダイレクトに生産現場に落とし込んでいる。
そのため、今回のように「顧客の要望を基にイチから設計を行う原設計担当者」と「組立性などの様々な要素を総合的に勘案して原設計を具体化する量産設計者」が現場で顔を合わせる機会が多々存在し、オンラインでは伝わりにくい細かい部分まで直接のやり取りが頻繁に行われるのである。
このように、より良い製品を提供するために年齢や社歴に関わらず気軽にやり取りができるDNLグループの開発環境が、若いうちからエンジニアとして活躍したいという希望を持つ彼女の成長を支えていたと言えるだろう。
原設計担当者の確認も経て、ついに製品の生産が開始した。想定よりも時間がかかってしまったものの教育係や周囲のフォローもあって、「自分が手掛けた製品を世に送り出す」という彼女の目標がついに実現しつつある。
目標達成を目前にした彼女が今回の挑戦への大きな手応えと充実感を感じながら日々を過ごす中、予想もしなかった事実が判明した。
次回、入社当初の目標を達成しつつある彼女に一体どのような結末が待ち受けているのか、目が離せない。
製品開発に携わる新入社員の瑠璃川が、1人前のエンジニアとして自身が手掛けた製品が世に出るまでを記す。
ゆえにこの連載は来月で終わるかもしれないし、10年かかるかもしれない。
Work at ADN -THE REAL-を通してADN発、新入社員成長ドキュメンタリーを紹介します。
2024年11月 配属16ヶ月目
瑠璃川はこれまで、ナットを締める電動ドライバーに取り付けるビットが間に合うかを確認しながら、組立方法の検証を続けていた。
生産開始予定日が近づく中、彼女の元にビットの外注先から連絡があったが、やはり量産開始の期日までにビットが届かないことが確実になった。
彼女は生産開始までの期日を考慮して、事前検証で検討していた案の1つである「ビットの代わりにボックスドライバーを使用して組立を行う」という方法で生産を進める決断をした。
事前検証で、多少工数が増えるもののデザイン性や品質面の問題がないことを確認していたため、すぐに量産段階に移行できた。
量産開始にあたっては、自身が原設計を手掛けた製品の最終段階を見届けるためにDNライティングの原設計担当者も立ち合いを行っており、案件を進める中で生じたお互いの疑問点や今後の要望など細かい点を意見交換することができた。
今回の特注案件は、既存の調光可能な製品に調色機能を追加するというものだった。
LED照明器具の光は器具内の基盤に取り付けられたLEDチップの色や明るさの違いによって変化する。しかし、LEDチップ自体に色味を変化させる機能はなく、チップは1色にしか光らない。
そのため、調色可能な製品にする場合は基板に色の違う2種類のチップを交互に配列する。
色を切り替えるつまみを回した時に違う色のLEDチップが光る設計にすることで、色の変化を実現するのである。
しかし、LEDチップへの電流の調整や切り替えを行う必要があるため回路設計がより複雑になり、調色機能がない製品と比較して電源装置本体が1.1~1.2㎝ほど大きくなる。
また、電源と基板を繋ぐ電線の数も増えてリードが太くなるため、組み立てる際に本体の中に収めづらくなってしまう。
顧客のニーズを製品に最大限反映するためにも照明器具本体の部材の大きさは変更できないため、リードの長さなどを微調整することで既存製品と同じ組立性を維持しながらデザイン性や品質を維持することができる。
当社に送られてくるデータでは顧客から出された要望をどのように原設計に反映しているか詳細には読み取れないため、今後より一層顧客のニーズに応えた量産設計を行うための勉強になったと彼女は語った。
DNLグループは、マザーファクトリーでもある当社を様々な角度から有効活用して顧客の声をダイレクトに生産現場に落とし込んでいる。
そのため、今回のように「顧客の要望を基にイチから設計を行う原設計担当者」と「組立性などの様々な要素を総合的に勘案して原設計を具体化する量産設計者」が現場で顔を合わせる機会が多々存在し、オンラインでは伝わりにくい細かい部分まで直接のやり取りが頻繁に行われるのである。
このように、より良い製品を提供するために年齢や社歴に関わらず気軽にやり取りができるDNLグループの開発環境が、若いうちからエンジニアとして活躍したいという希望を持つ彼女の成長を支えていたと言えるだろう。
原設計担当者の確認も経て、ついに製品の生産が開始した。想定よりも時間がかかってしまったものの教育係や周囲のフォローもあって、「自分が手掛けた製品を世に送り出す」という彼女の目標がついに実現しつつある。
目標達成を目前にした彼女が今回の挑戦への大きな手応えと充実感を感じながら日々を過ごす中、予想もしなかった事実が判明した。
次回、入社当初の目標を達成しつつある彼女に一体どのような結末が待ち受けているのか、目が離せない。